Unimec Fabrikations AG
This Swiss company has been producing metal components for demanding customers for 20 years. Today, Unimec Fabrikations AG houses a production space of around 6,700 square meters and 85 employees in Wetzikon, Zurich. Jonas Locher, member of the board at the family-owned company, summarizes the company philosophy in two sentences: “Our orders are always special requirements. That’s why we are never satisfied with reaching the standard.”
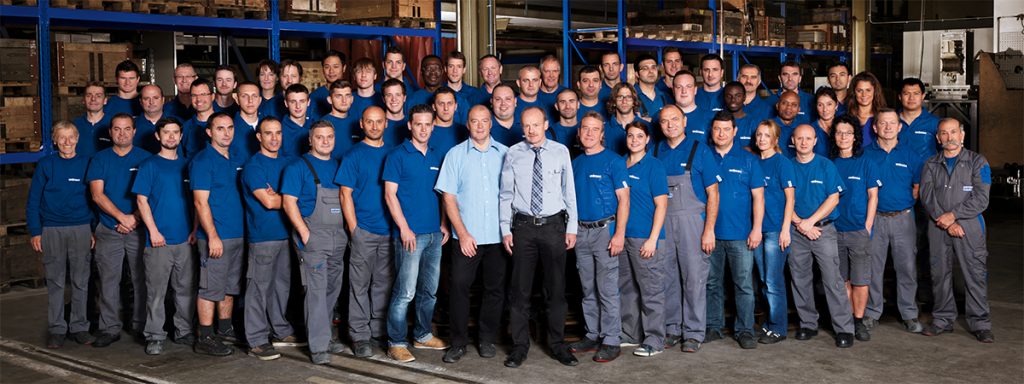
The challenge in the industry
In 2014, Jonas Locher realized that things could not continue as they were; meeting the ever increasing demands of customers was becoming more and more challenging, not in terms of quality, but with regard to traceability and documentation. Customers from industries that were relevant to security, such as air travel, nuclear technology and railway vehicles, were growing ever more demanding. “Documentation obligations have increased massively in the last ten years. We sometimes had to provide a half a folder of paper with one single component. Our customers also wanted to view documents again years later, and we needed more and more time to find and supply documents.” The company ultimately needed a solution for accessing documents rapidly.
We got to see how customer-focused adeon ag operates. It involves itself with our issues and finds the right solution for every work step. That never ceased to amaze us.
Jonas Locher
Member of the Management Board
unimec fabrikations ag
Making the physical storage of documents redundant
Unimec began to search for such a solution – and found it in the company adeon ag and its document management software d.3ecm from d.velop. Previously, Unimec had stored everything in paper form: “Invoices, delivery notes, order confirmations, production records, material certificates, as well as measurement, machine, welding and test logs …” Jonas Locher explains with exhaustion. The requirements for d.3ecm were quickly formulated: the software needed to make the physical storage of these records redundant; employees were to be able to access documents on their computer with just a few clicks. Jonas Locher sat down with the adeon project team led by Andreas Kradolfer with those aims in mind. Jonas Locher explains: “Mr. Kradolfer and his team visited us and took a close look at how we worked. To begin with, we just knew that we needed a document management solution. Now, we worked together to define the file structure, determine which documents needed to be linked to each other and come up with a practical method for storing them so that we could find them again at any time with a few clicks of the mouse.”
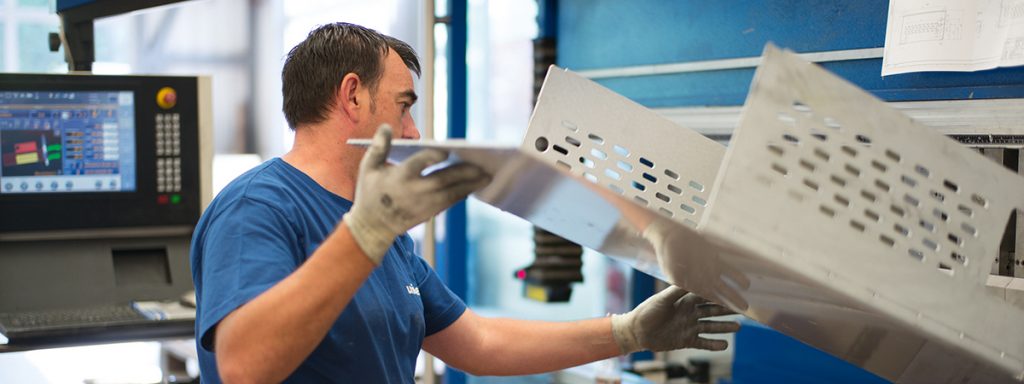
Unimec processes around 1,000 production orders per month. One single order can fill up to five DIN A4 pages with various records and, naturally, invoices, order confirmations, delivery notes and more. Previously, an order was processed as follows: the orders were recorded on a computer in the work preparation department, and the components were drawn in design. Once everything was in order, the project processor handed the order over to production. All the documents belonging to an order were transported from station to station along with the order and the components. They were checked in production and provided with any number of notes and calculations by the processors. At the end of a production process, staff sent the documents back to the office, where they were stored in folders.
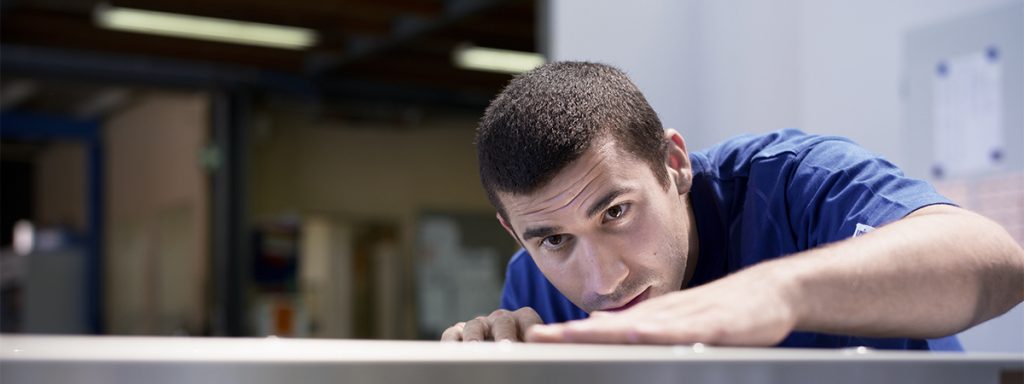
Bar codes assign every record to an order
The company adeon proposed a pragmatic approach for stemming the floods of paper in the future. Since documents still needed to be signed to ensure traceability, the simplest method was to provide them with bar codes. Every document could then be clearly assigned to an order – regardless of whether it was created by the normal Unimec ERP software or with word processing software. The open architecture of the d.3ecm document management solution meant that Unimec’s requirements could be dealt with in a systematic way. Step by step, adeon adapted the range of services in the new d.3ecm solution to Unimec’s work processes. As a result, it integrated seamless into the company’s established work flows – and Unimec could continue to use the ERP solution and all the other software applications that it worked with without any issues. d.3ecm simply enriched the existing solutions with a system for storing all the documents related to an order, no matter which program they were created with. Staff can use it to find any document again instantly, from the order confirmation to the delivery note – and even directly from the ERP software.
Great time savings, great enthusiasm
With the new d.3ecm solution, production staff can still make notes on production papers like before, and then sign and submit them once the task is complete. Once the paper record has fulfilled its purpose, it is forwarded to the office – and just has to be scanned in there. The bar code automatically assigns it to the right order with the right name. The paper can now be discarded. There is just one small exception, explains Jonas Locher: “The nuclear industry. It needs the original documents to be retained. No problem! We scan them in the same way as all the other documents here – and then send them to the customer. That completes our end of the bargain; we keep the scan. And we can now discard everything in paper form.”
Access to every document in just a few clicks
Unimec staff are delighted with the new system. They no longer have to store anything in production folders, and can access all the documents through the computer system. Processors benefit from the major time savings as a result. Jonas Locher estimates that it previously took
around two hours of effort per week and per person to store documents and find them again. “The unbelievable flood of documents was becoming unmanageable. We now have everything under control. We know exactly where the documents are stored and can access them at any time. It works perfectly.”
The rollout of the new d.3ecm solution was completed by the middle of 2015. One of the best compliments that his company has received in the meantime was from an important customer from France – a customer from the nuclear industry, as Jonas Locher explains:
This customer visited us some time ago to see for himself whether we were the right place for his production orders. We had already supplied him with components many years ago. During his discussion with us, he suddenly took one of these components out of his pocket and put us to the test. A production number was engraved onto the part. He asked us to show him the documents with the material certificate for that production order. One of our staff left the room, sat down at a computer and printed out the documents – and handed them over to the customer four minutes later. He could not believe it. He was completely stunned. Before the introduction of d.3ecm, we would have had to find out which year the part was produced, then log into ERP to access the archive and finally dig out the documents. Of course, such an order can easily contain 200 individual parts – we would have had to search for two hours before finding the papers.
Jonas Locher
Member of the Management Board
unimec fabrikations ag
The fact that production documents in the nuclear industry need to be stored for 30 years made the whole issue even more vital. That is also no longer a problem thanks to the new document management solution.
Another brilliant system for managing measuring devices
Unimec was so impressed by d.3ecm that they immediately gave adeon a subsequent task: a solution for managing measuring equipment. Around 4,000 measuring devices, from caliper gauges to 3D measuring machines, are in use at the company. Thanks to the new system, which adeon based on bar codes developed especially for Unimec, the company can now track when and with which measuring devices a product was manufactured. This traceability is particularly important in air travel, to prove the flawless calibration of measuring devices used for the production of a component. Jonas Locher says: “The measuring equipment management solution is another brilliant system that adeon has built us.”
The d.3ecm document management system has been fully integrated at Unimec for a long time now. However, Jonas Locher is already thinking ahead. For the future, he envisages a switchover to paperless operation in production for the over 10,000 orders the company receives per year. “We want to continuously add more areas to make our work even more efficient – for instance, by scanning in supplier invoices or filling out order documents in production automatically.” It is clear to him that adeon should also be on board here. “We got to see how customer-focused adeon ag operates. It involves itself with our issues and finds the right solution for every work step. That never ceased to amaze us.” And he emphasizes once again how happy his company is with both the collaboration with adeon and the d.3ecm solution from d.velop.
The project partner:
adeon ag is a committed team of highly-qualified and experienced specialists who develop and implement innovative solutions in the fields of document management, electronic archiving and workflow (Business Process Management, BPM). Sustainable process optimizations need a competent partner. The adeon ag team applies its knowledge and many years of experience in a systematic way to closely analyze problems, define in-depth concepts and precisely coordinate their implementation. adeon ag is the competence center for ECM solutions for d.velop and, in its role as managing distributor, is responsible for the markets of Switzerland and the Principality of Liechtenstein.