Preserving knowledge: KIMW uses AI to make expertise from 15,000 test reports digitally accessible
The Kunststoff-Institut Lüdenscheid (full name: Kunststoff-Institut für die mittelständische Wirtschaft NRW GmbH, KIMW) is a privately operated technical service company founded in 1988 as an extended service arm and research institute for the plastics processing industry in South Westphalia. Based in Lüdenscheid, the institute collaborates closely with the local university of applied sciences and employs around 100 staff members. These experts support companies in the plastics industry through research, development, training, and consultancy services, with a particular focus on failure analysis, material, and process optimisation.
While deeply rooted in the South Westphalia region, KIMW also operates on a national and international level. For instance, it conducts process optimisation projects and training sessions in countries such as China, Korea, Canada, and the USA.
d.velop pilot
Product
100
Employees
Technical services
Industry
KIMW: Damage analysis requires extensive expertise
Damage analysis is a specialised field that holds great significance at the Kunststoff-Institut Lüdenscheid (KIMW). The institute’s experts investigate defective or broken components sent by clients seeking to identify the root cause of failures. A typical question the team aims to answer might be: Why did this particular component fail?
Technical root cause nalysis on behalf of clients
“This isn’t always due to client error,” explains Jörg Günther, Managing Director of KIMW Prüf- und Analyse GmbH. “In many cases, the issues are production-related.” The task, therefore, involves using experience and consulting with technicians to determine why, for instance, a galvanised component has developed a blemish. In short, it is about conducting technical root cause analysis, forming a hypothesis, and attempting to validate it. This process often requires extensive expertise, as “sometimes you’re searching for a needle in a haystack.”
Fluctuation threatens knowledge preservation
The KIMW handles approximately 3,400 such processes each year. Each concludes with a comprehensive inspection report containing valuable information and insights. However, a key issue emerges in this process: “Due to the economic fluctuations caused by the pandemic, generational changes, and the persistent shortage of skilled professionals, we are experiencing a level of staff turnover that results in a significant loss of knowledge,” explains Jörg Günther. “It takes a great deal of time to recruit and train new employees.” In some areas, replacing 20 years of professional experience is a formidable challenge. Hiring new personnel requires at least six months or more of training—despite solid educational backgrounds.
Since 2010, Kunststoff-Institut has digitally stored all 15,000 reports
To address this issue, the KIMW initially turned to improved knowledge management. “We introduced a new nomenclature and other measures, but in the end, it all meant double the work,” reflects Jörg Günther. The critical question, or “pain point,” became: “How can we preserve our concentrated knowledge?” One significant advantage for the KIMW is that “since 2010, we have been storing all our reports in digital form within our IT systems.”
Using DMS and AI to secure knowledge
Digital archival documents hold a wealth of information, as Jörg Günther knows well. However, he explains, “There are around 15,000 reports, and searching through them by keywords with the existing tools was quite inefficient.” A fortunate coincidence changed everything: “As the Kunststoff Institute, we are a member of the infpro association (Institute for Production Preservation). During one of infpro’s Value Creation Days, a board member from d.velop gave a talk that inspired us to archive and utilise our knowledge using a document management system (DMS) combined with the AI tool, d.velop pilot.”
Storing all reports in the DMS and asking AI content-driven questions
“That was a stroke of genius,” recalls Jörg Günther. “It was exactly the solution we needed. We could upload all the reports into the DMS and then ask the AI content-driven questions, rather than merely filtering or sorting the data.” The key advantage, he notes, is, “I don’t have to do anything with the reports. I don’t need to review or process them to make them usable.”
Clearly defined vision for future AI use at KIMW
At the event, Günther approached the speaker from d.velop directly: “We had a brief discussion, and I later reached out to d.velop again to outline our specific challenge.” To clearly articulate the objectives for the planned AI deployment, Günther prepared a one-pager listing all the desired functionalities. “The team at d.velop appreciated it because someone had a clear vision of what they wanted to achieve with their AI and even provided a proposed solution.” The collaboration progressed swiftly from there.
Key topic: ensuring the confidentiality of customer data
A pivotal aspect of the implementation and a core requirement for using the AI was ensuring the security and confidentiality of client data. “These reports contain sensitive information,” Günther emphasises. “They might detail how Company XY commissioned an analysis to investigate damage YZ.” Maintaining strict confidentiality is critical, he insists. “Feeding such a report into an AI like ChatGPT is out of the question, as there’s no way a damage analysis report containing real names could be allowed to circulate online.”
d.velop is working with a lot of manpower on a solution for the Kunststoff-Institut
To address these concerns, the Kunststoff-Institut Lüdenscheid requested that the system managing the test reports accessed by d.velop pilot be installed on a completely isolated platform, ensuring no external access. “d.velop committed significant resources, energy, and speed to implementing the solution,” recalls Jörg Günther. He admits that the pace of d.velop’s work was sometimes difficult to match internally: “After all, we still have day-to-day operations to manage.”
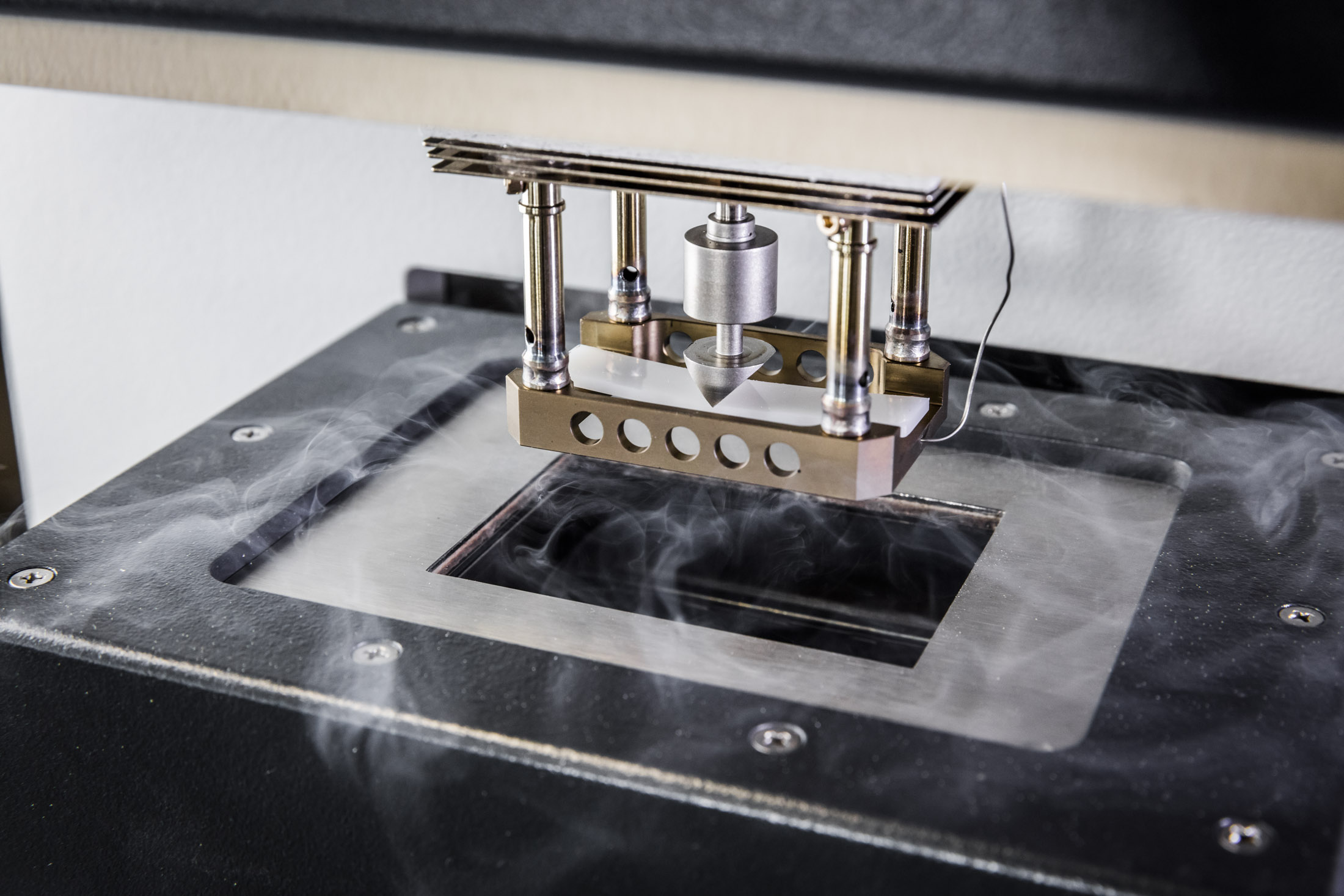
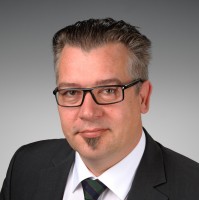
I was extremely positively surprised by our collaboration, particularly by the fact that we had a comprehensive preliminary meeting. The team from d.velop arrived with a whole group and first took the time to clarify what we actually wanted and needed.
Jörg Günther
Managing Director
KIMW Prüf- und Analyse GmbH
Exciting kick-off meeting Impresses KIMW
“We received our test access quite promptly,” says Günther, adding: “There was one thing I hadn’t anticipated: I was extremely positively surprised by the way we collaborated. We held a large preliminary meeting on-site, and d.velop brought an entire team to clarify exactly what we wanted and needed.” He continues: “What really impressed me was their approach of thoroughly evaluating whether our envisioned goal even made sense to pursue in the proposed manner.” Günther sums up with satisfaction: “Such measures and this approach are excellent for engaging employees and generating enthusiasm for a project.”
d.velop DMS as a standalone solution for AI
For several weeks now, the AI-powered d.velop pilot has been live and operational. “We decided to trial it for 12 months, but if we didn’t see any benefits, we wouldn’t have moved forward,” explains Günther. Damage analysis reports are now stored in the d.velop documents document management system (DMS), used exclusively as a standalone solution for the AI. The DMS functions as a self-contained ecosystem. “We upload our reports, and the system keeps learning.” Using the standard DMS interface, users make a preliminary selection before querying the system with the help of AI.
AI provides verifiable sources
One major advantage of the d.velop pilot is its ability to cite sources directly. These are summaries based on indexed reports, ensuring that the large language model (LLM) does not simply string together words or rely on potentially invalid sources. This keeps the AI closely aligned with the reports at hand. “Even if I’m skeptical about an AI-generated result, I can click directly on the associated reports. It’s a system we can work with,” says Jörg Günther. “Those using it, including new employees, are highly qualified individuals—chemists, bachelor’s and master’s degree holders, or even PhD graduates. While they need to be trained on specific topics, they are more than capable of making sound judgments,” he asserts. Additionally, users can explore the system for solutions on a trial-and-error basis, especially since 90 % of daily operations involve standard tasks. “This often leads to solutions that might not have been immediately obvious,” Günther notes.
Kunststoff-Institut Lüdenscheid to trial d.velop pilot for 12 months
Given the high volume of damage analysis cases annually, “the AI could easily be used multiple times a day,” Günther estimates, highlighting the potential of AI at the Kunststoff-Institut für die mittelständische Wirtschaft (KIMW). This potential will now be tested. “We activated the paid access this month for a one-year period to validate and rigorously test the system. I’m optimistic that I won’t need to persuade my colleagues to try it—they’ll need to convince themselves of its utility,” Günther explains. No extensive training was required to use the d.velop pilot. “The underlying system is essentially a search function with specific filter criteria.”
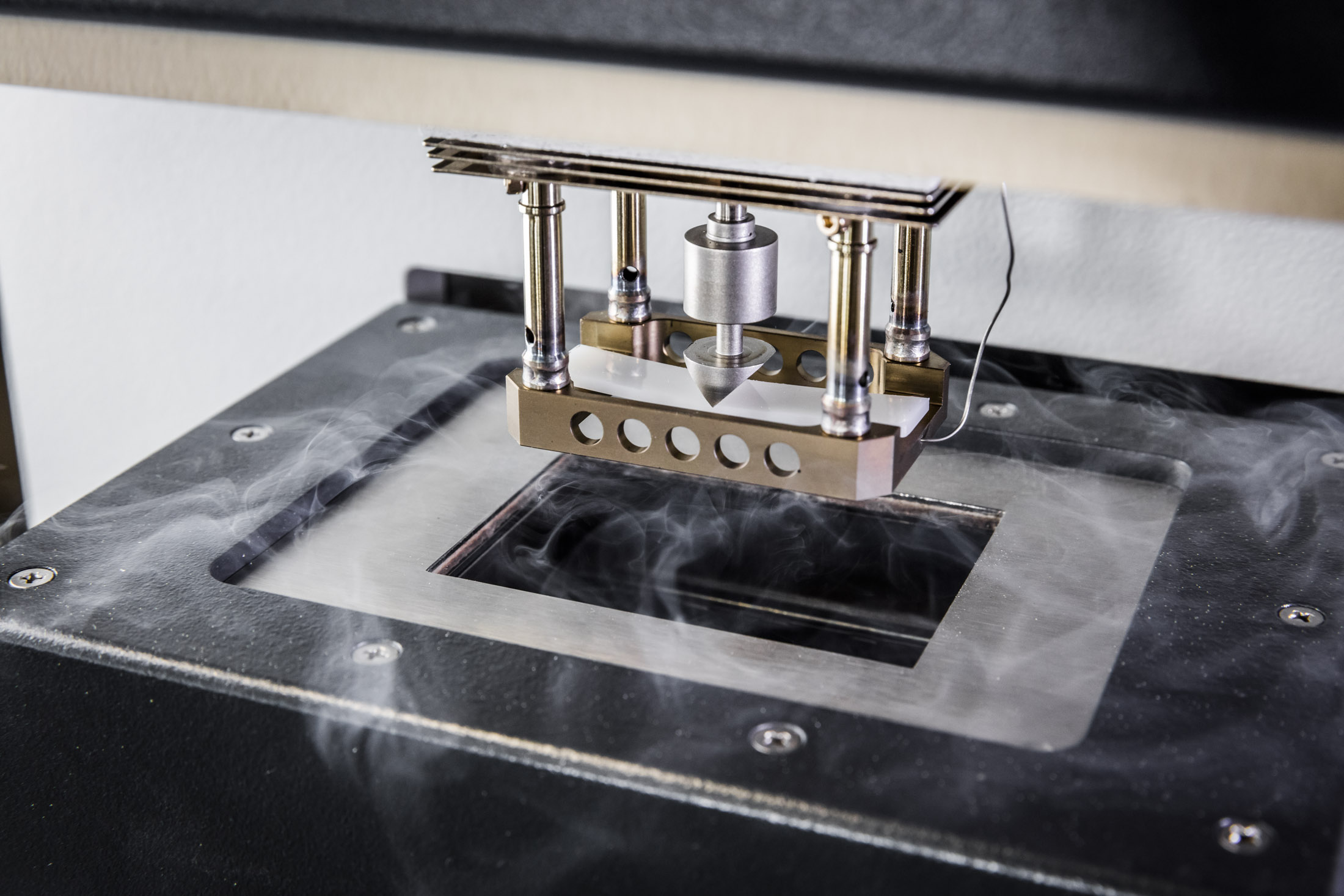
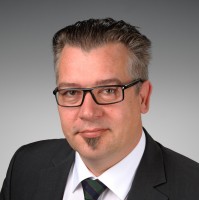
I am one of those people who are often asked whether we have already worked on a particular topic and where the results can be found. As long as people can ask me, everything is fine. However, if that’s no longer possible, a lot of knowledge will be lost unless there’s a technological solution in place by then.
Jörg Günther
Managing Director
KIMW Prüf- und Analyse GmbH
Vision of opening the KIMW database to external partners
The hope of having found a solution for the efficient preservation and utilization of company knowledge is high. Equally strong is the confidence that the d.velop pilot could succeed. “I’m one of those people who is frequently asked whether we’ve worked on a certain topic before and where the results might be stored. As long as people can ask me, it’s fine. But if that’s no longer possible, a lot of knowledge will be lost unless there’s a technological solution in place by then.” Jörg Günther’s vision of an AI-supported database grows with the opportunities such a solution could bring to him and the institute: “Perhaps one day, this could be opened up as a digital business model,” he suggests. “Partner companies and subscribers could then access our extensive knowledge.” However, the aspect of data protection would first need to be clarified. In other words, the documents would need to be anonymized.
Accumulated knowledge of the Kunststoff Institut is highly valuable
The KIMW has repeatedly considered how to commercialize its knowledge. However, the idea of possibly publishing it as a book never seemed groundbreaking. “You can’t make much money with books these days,” says Günther, but he adds: “If I have a comprehensive knowledge database that contains the collected expertise of the Kunststoff Institut over the past 30 years on various specialized topics, that’s incredibly valuable.”
Positive feedback after initial weeks of use
What’s the initial verdict after a few weeks of use? “It’s certainly not the case that we’re suddenly generating ten times the revenue or halving processing times,” summarizes Jörg Günther. “But the initial feedback on working with the d.velop pilot has been consistently positive.” Of course, the tool must first establish itself in daily operations, but “it’s relatively new, and so far, I’ve only heard good things about it.”
Software Demo
Get to know d.velop Software
Would you like to experience our SAP solutions live?
Simply fill out the form and request a software demo.