We continue our series of blog entries about the digital procurement process in SAP. After talking about the entire procure-to-pay process and focusing on the SAP purchase requisitions, we are going to look at the SAP incoming goods process – since a successful purchase order will hopefully be followed by prompt delivery of the requested goods.
This is the point we have reached within the SAP procurement process in the meantime.
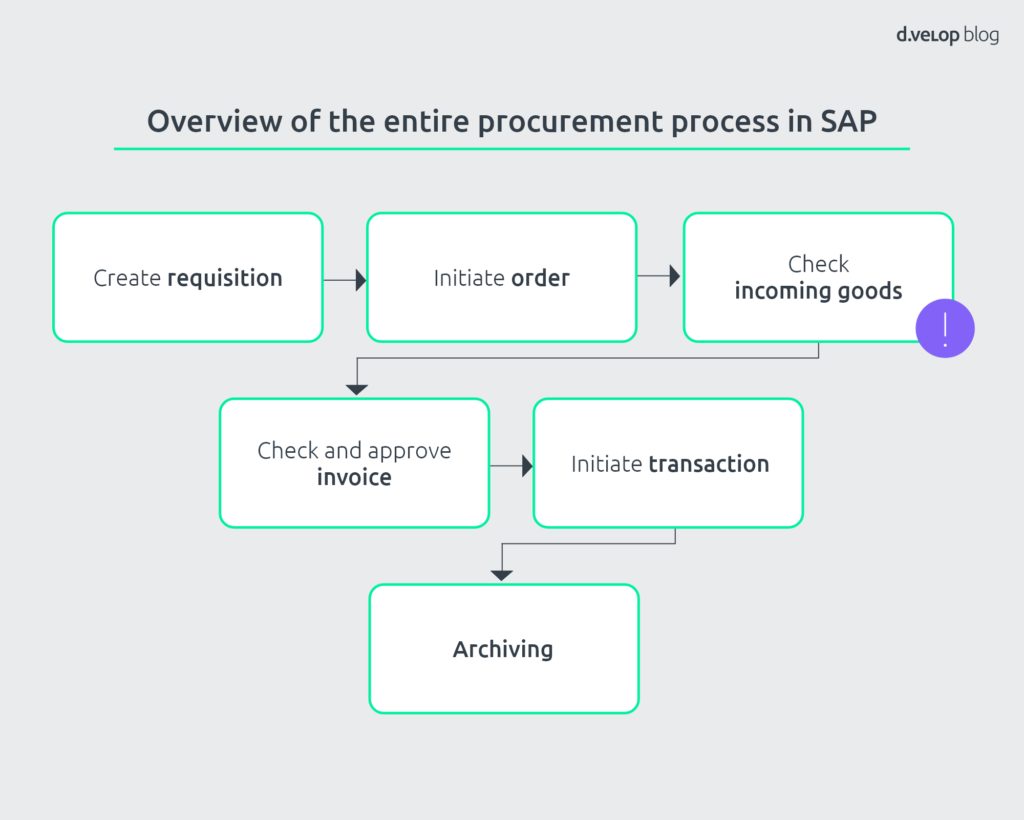
Verifying incoming goods in SAP – the right goods in the right place, at the right time
When it comes to incoming goods, you need to check whether the delivered goods have been received in the right quantity and quality as well as at the right time and place within the company as quickly as possible. At this point in the process, you should review and document the following questions:
- Has the delivery/goods shipment arrived?
- Is the delivery complete and free from defects?
- Can the incoming goods be posted?
- Can invoice verification in logistics be performed?
- How can I assign the delivery note to the order and then to the invoice?
At first glance, this seems to be a demanding, but not impossible task. To get a feel for the complexity of verifying and inspecting incoming goods, let’s consider an example:
A company orders goods through its headquarters in Frankfurt. The goods are subsequently delivered to Frankfurt and subsidiaries in Munich and Hamburg. At each location, the incoming goods are checked and then accounted for on the delivery note. Only after each delivery note has been received by headquarters the incoming goods can be documented, albeit late.
As you can see, even relatively minor factors such as multiple subsidiaries can complicate the incoming goods process in SAP. Just imagine then how error-prone and inefficient a non-automated incoming goods process might be. We are going to stay true to the structure of our series of blog entries and compare a non-automated with an automated, i.e. digital SAP incoming goods process.
Paper-based incoming goods process: Potential risks everywhere
A traditional, paper-based incoming goods process in SAP consists of numerous separate manual steps. Once the incoming good have been received, their completeness and quality must be checked. If the goods are acceptable, the acknowledged delivery note is placed in the pigeonhole and forwarded to Purchasing or headquarters via in-house mail. This is the first delay in the process.
After the documents have finally arrived at the right location within the company, the incoming goods are recorded manually. The responsible employee must search within SAP for the correct purchase order and post the incoming goods. Because there is such a large amount of manual entry involved at this step in the process, it is often where errors occur. These errors can have far-reaching consequences for other departments such as finance and invoicing.
In the next step, the delivery note still needs to be manually assigned to the initial purchase order and records need to be stored in a location in close proximity to employees so that they can be quickly accessed, which leads to space and coordination issues.
After the incoming goods have been received, the company must still deal with a bevy of maintenance tasks since tables generally need to be updated to track current information about the incoming goods. In general, non-automated incoming goods are extremely time-consuming and prone to error. Throughout the entire process, the danger of losing delivery notes, records, or notes is high. Reason enough to think about automation of incoming goods.
Digital incoming goods process: Record and post deliveries in real time
In contrast to the traditional process, delivery notes are scanned and recorded in the automated process right after the incoming goods have been received. OCR recognition is used to read delivery notes and relevant data, including supplier, order number, and order quantity, which is directly transferred to the SAP system. You can use workflows to electronically forward data from the delivery notes to the appropriate colleagues for processing. During this process, the delivery note is archived in an audit-proof manner.
A direct link to the underlying purchase order in the digital process is a major boon. The purchase order and incoming goods are automatically reconciled during scanning and linked together. During this process, the items in the order are reconciled with the incoming goods so that employees in the goods warehouse or purchasing can instantly recognize if the purchase order is complete and then record the incoming goods. When it comes to raw materials that are critical for production, a multi-stage approval process can be implemented so that only authorized employees who are able to obtain an overview of the entire process can post the incoming goods. This way, each person involved in the process has a comprehensive overview of the current incoming goods. It takes just a few automated steps to enter and post the incoming goods in SAP.
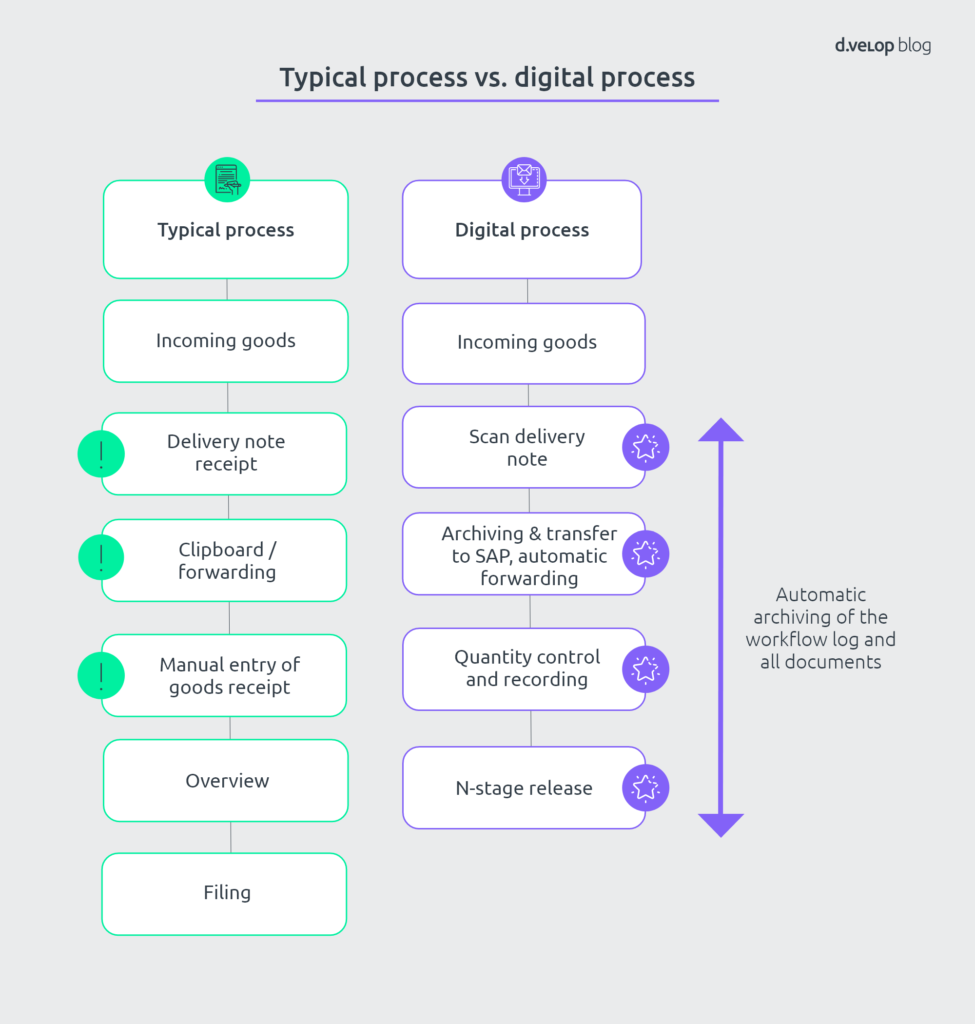
Overview of the benefits of digitally inspecting incoming goods
- Immediate overview of incoming goods
- Rapid verification and direct posting of deliveries in SAP
- Acceleration of downstream processes, especially of incoming invoice processing in logistics
- Automatic delivery note archiving
Since the benefits are clear now, the only thing that lacks is the right solution. With the overview of your incoming goods provided by d.velop delivery note for SAP ERP, you know right away when a delivery has arrived in the decentralized warehouse. The delivery can be checked and the corresponding material document for the delivery can be entered directly into SAP and then posted. You can find all the information on our page about the digital procurement process in SAP.