Efficient process management is the key to a successful and competitive company. However, not only the implementation and introduction of business processes, but also ongoing process optimisation in your own business environment brings countless benefits.
What are the benefits of process optimisation?
The advantages of process optimisation can include
- Reduction of costs and resources
(e.g. reduction in material usage or water/electricity consumption) - Improvement of process quality
(e.g. planning accuracy & risk avoidance) - Increase in process speed
(e.g. by shortening the production time) - and increasing employee satisfaction
(e.g. through better working conditions) - and ensuring customer satisfaction
(e.g. through better product quality and availability)
Reliable and optimised processes are essential for the existence and further development of a company. A company can only be successful in the long term if these processes function smoothly and efficiently.
How important is process optimisation in companies?
The importance of process optimisation and process organisation in companies is constantly increasing – also due to external influencing factors that SMEs in particular have to face. These include increasing competitive pressure due to globalisation, individual customer requirements and increased market demands on products and services. Demographic change, the associated ageing of the workforce and the resulting loss of knowledge are also challenges that many companies are facing.
Product innovation vs. process optimisation
There are often 2 answers to react to or counteract these influencing factors:
- Product innovation
- process optimisation
The latter refers to internal company structures. These are often more sustainable than product innovations, but often only take effect later or with a time lag. Generated and perceived benefits therefore only become visible and measurable later.
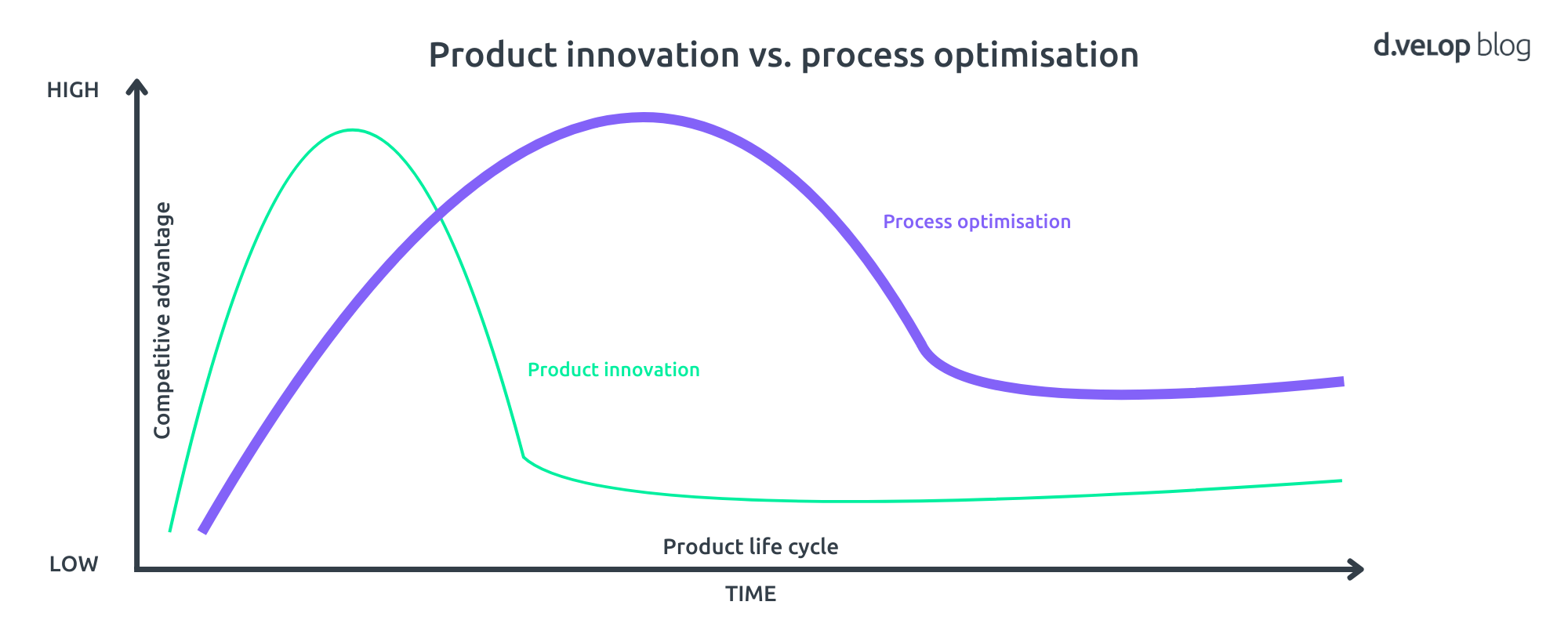
Processes become the new corporate gold
Another advantage: as processes are often customised and precisely tailored to the company, they cannot be copied by the competition, as is the case with product innovations. This makes processes the new corporate gold.
However, this realisation has not yet penetrated every company. In some cases, there is a lack of awareness of this issue. A lack of understanding at management level, methodological knowledge – but also responsibilities (e.g. in the form of an explicit role in the company) are just some of the common obstacles when it comes to optimising processes.
This blog article will give you an initial overview of what is meant by a (business) process, how you can identify these in your company and how you can carry out successful process optimisation in 4 steps.
What is a process?
Processes (term from the Latin: ‘procedere’, to proceed, or ‘processus’, the course or progress) are also referred to as operations, sequences or work steps. According to ISO 12207, a process is ‘a set of interrelated means and activities that transform inputs into outputs. Processes are often broken down into sub-processes’.
If you take a closer look at the DNA of a ‘process’, the definition quickly becomes clear. A process indicates that something is to be carried out in a certain way (with one or more activities) in order to produce a desired result at the end. It promises consistent and lasting quality and efficiency.
How can I recognise a process?
A process consists of essential characteristics that are the same. The following characteristics can be used to clearly determine whether it is a process:
- Structured: A process has a certain structure and defined steps that must be carried out one after the other.
Example: I first have to knead dough before I can bake it. - Goal-orientation: A process has a specific goal that is to be achieved, such as the manufacture of a product or the provision of a service.
Example: The goal is to make a waffle. - Repeatability: A process is designed to be carried out repeatedly in order to achieve the same result.
Example: I can make the same waffles exactly the same way over and over again. - Measurability: A process can be measured to assess its efficiency and effectiveness.
Example: A waffle iron can produce 30 waffles per hour. - Controllability: A process can be monitored and controlled to ensure that it achieves the desired result.
Example: The baking time of the waffle takes exactly 2 minutes at 220 °C. - Flexibility: A process can be customised to adapt to changing requirements or conditions.
Example: Fresh blueberries are added to the waffle batter as an ingredient to produce a new waffle flavour. - Documentation: A process is documented to ensure that it is carried out in a uniform and standardised manner and to provide a basis for improvements and optimisations.
Example: The recipe for a precise waffle production process is available. - Customer orientation: A process is designed to fulfil or exceed the needs and expectations of customers.
Example: The goal is a delicious waffle that everyone likes and children love. - Collaboration: A process often requires the collaboration and coordination of different people, departments or organisations to achieve the desired result.
Example: The chicken has to lay the eggs 😉; The raw materials only come from the organic farmer I trust; The waffle iron has to be maintained and cleaned; The baker has to be able to operate the waffle iron and the oven; etc. - Improvability: A process can be continuously improved in order to increase its effectiveness and efficiency and increase customer satisfaction.
Example: I buy a second waffle iron so that I can produce more waffles or use higher quality ingredients from the organic shop.
And this is precisely where you can start to identify potential for optimisation. So how do you find levers that change the process and make it better?
Definition of process optimisation
Process optimisation is a systematic approach to improving existing processes. Process optimisation comprises 4 steps:
- Identification & documentation using a process map
- Process analysis
- Process redesign
- Process implementation
Process optimisation: How it works in 4 steps
Discovering an error in the process by chance and correcting it is not process optimisation. It requires a systematic, methodical approach. So what can such an approach look like? Process optimisation can be achieved in 4 steps. All steps ultimately serve to derive an (improved) target process from an analysis of the current situation.
1. Identify and document processes with a process map
Albert Einstein once said that ‘recognising the problem is more important than recognising the solution, because the exact representation of the problem leads to the solution.’ Before you can optimise processes, you must first identify and document them.
A good way to do this is to use your process organisation or organisational chart to create a process map that shows all processes and their dependencies. This will give you an overview of all processes in the company. The creation of a process map should be carefully planned and approached, as it represents the starting point for further process mapping, analysis and optimisation.
What should be considered when creating a process map?
- Define the purpose and scope of the process map. Think about which processes you want to include and which goals you want to achieve with the process map. For example, do you only want to include the company’s core processes or also supporting processes such as HR or IT?
- Identify the processes that need to be included in the process map. Gather information about the various processes in the company, e.g. by conducting interviews with employees, using creativity techniques such as brainstorming, mind maps or the 6-3-5 method, analysing documentation or organising open-ended workshops.
- Categorise the processes. Think about which processes have similar goals or results and categorise them accordingly. This can be done by department, function or business process, for example.
- Visualise the processes. Use symbols and diagrams to visualise the processes in the process map. There are various options, such as flowcharts, swimlane diagrams or BPMN diagrams.
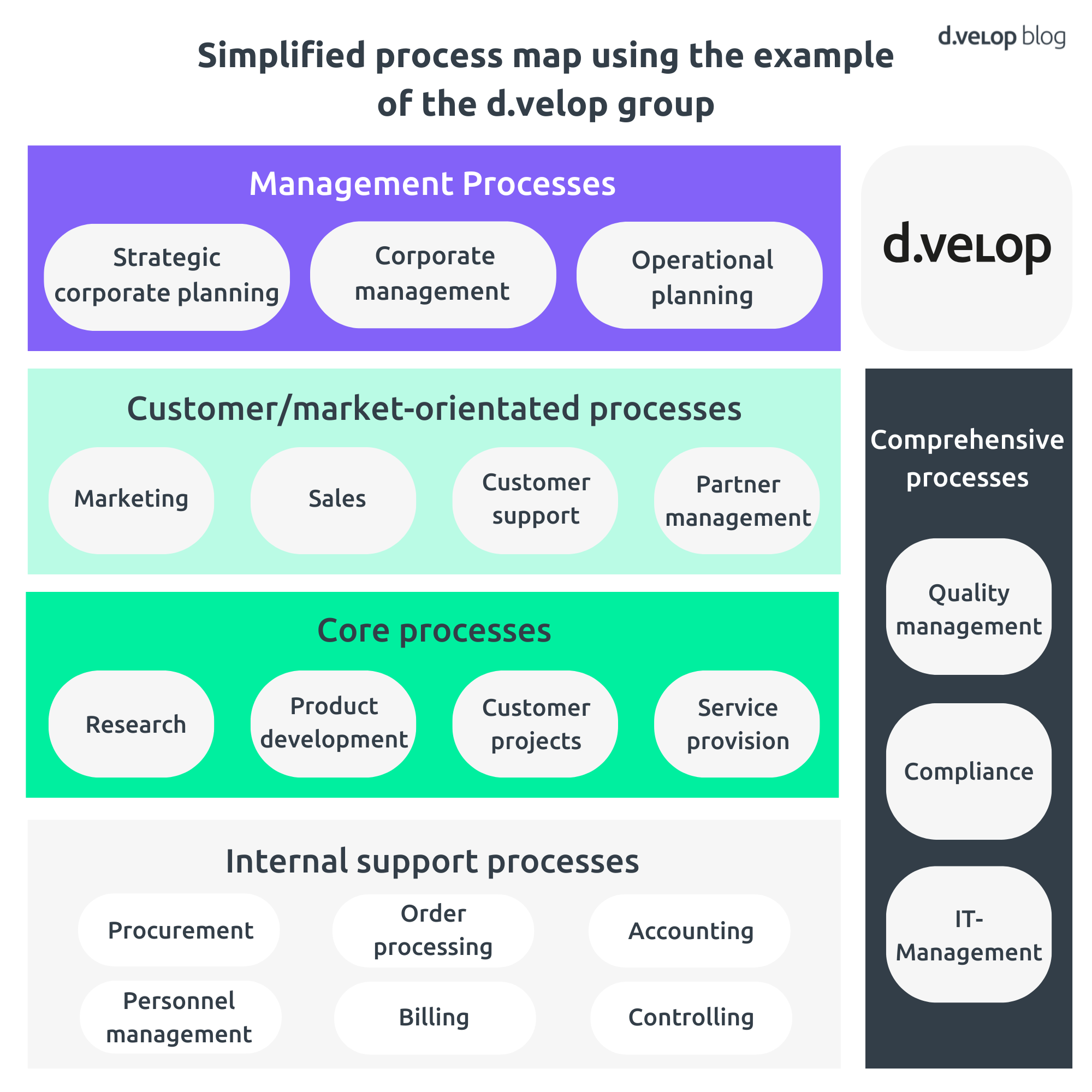
Then document the current status of your processes. Add descriptions and further information on the individual processes to better understand their functions and interrelationships.
Tip for the future
Once your map has been created, the lion’s share of the work is done. Now it’s time to review and update the process map regularly. Processes can change over time – in times of digitalisation, this mainly affects supporting IT processes and system landscapes, which is why it is important to regularly review and adapt the process map.
2. Analyse processes
Once you have identified the processes, you should analyse them. This involves identifying weak points and bottlenecks and understanding how the processes run. Process KPIs should be defined here in order to measure and compare the performance of processes. Examples of process KPIs are
- Throughput time
- error rate
- productivity
3. Redesign processes based on the analysis
Now it’s finally (!) time to get down to business and the most difficult part follows: implementation. As soon as you have identified weak points and bottlenecks in your processes, you can optimise them. There are various approaches here, such as Lean Management, Six Sigma, Business Process Reengineering (BPR) – just to name a few.
- Lean management is about eliminating waste and making processes leaner. It should only do things that create value for customers. Processes that do not contribute to value creation must be abandoned.
- Six Sigma, on the other hand, focuses on reducing errors and variability in processes and focusses more on a continuous improvement approach. With this method, key figures are defined for each process, which can be used to measure the impact of improvements.
- Business process reengineering (BPR) is used in particular when business processes are to be radically redesigned, especially in established companies that have hardly changed over a long period of time.
4. Implement and monitor processes
Once you have optimised the processes, you should ensure that the improvements are also implemented. It is important to define clear responsibilities and process descriptions. Regular checks and reviews should also take place to ensure that the processes continue to run efficiently.
Where is the best place to start with process optimisation?
The automation of routine tasks, hyperautomation or process digitalisation in general can be a particularly effective way to optimise business processes. Why not start with the document processes in your company? These are often a good place to start in order to realise potential. For example, you can realise the following exemplary processes:
- Approval process
- Procurement request
- Holiday application
- Booking process
- Incoming invoice processing
- Damage report
Below you can see how to set up a simple authorisation process.
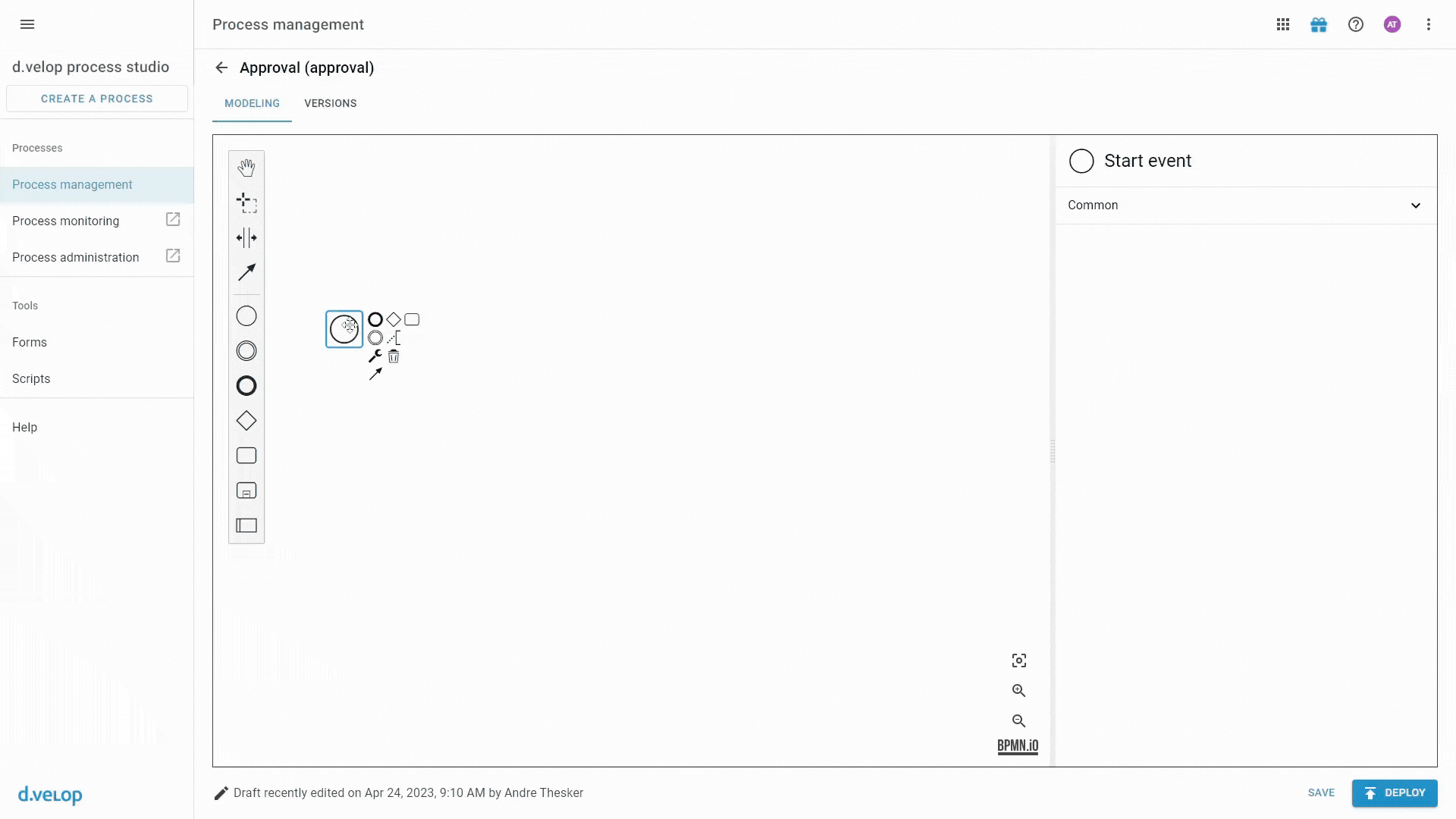
💻 Software demo for the d.velop process studio
Book your individual software demo for d.velop process studio in our document management system with just a few clicks. Let our experts give you a live demonstration of the software and ask your questions about modelling business processes directly.
How can tools such as the d.velop process studio support process optimisation?
The d.velop process studio is the central entry point for the topic of process automation within the d.velop platform. The d.velop process studio consists of several components and tools that support you in digitising, automating and documenting your day-to-day work.
In the d.velop process studio you have the following options for process optimisation:
- Modelling
- Automate
- Documenting
- Logging
- Monitoring
What is your learning?
Optimise your processes! It is important to identify, analyse, optimise and implement processes. Although this requires a certain amount of effort, it offers companies the opportunity to familiarise themselves with their own processes and scrutinise them. With regular checks and reviews, companies can ensure that their processes continue to run efficiently and are continuously improved.