Process management is an essential part of efficient business management. It ensures that all processes in a company are structured, optimised and continuously improved. In this blog article we look at the topic of process management and explain why it is so important for companies. In addition to the goals, we also look at the advantages and the process management methods.
What is process management?
Process management plays a crucial role in today’s corporate world by helping to optimise processes and make them more efficient.
Definition of process management
Process management is the systematic planning, control and optimisation of business processes, in order to improve their efficiency, quality and effectiveness. It includes the identification, documentation, analysis and their continuous improvement, in order to use resources more effectively, reduce costs and increase customer satisfaction.
Process management is aimed at creating clear structures and responsibilities within the organisation, eliminating weak points and increasing overall performance. It ensures that processes meet company goals and customer requirements.
Classic vs. digital process management
The difference between classic and digital process management lies in the way business processes are recorded, designed and optimised.
In classic process management, the documentation and analysis of processes is often done on paper or in static documents. Changes and improvements are time-consuming and require manual updates.
In contrast, digital process management enables the use of software solutions to model, monitor and adjust processes in real time. This enables faster response to changes and improves transparency. Additionally, digital process management tools can offer automation features that further increase efficiency. Companies that rely on digital process management are able to work more agilely and cost-efficiently, offering a potential competitive advantage in an increasingly digital business world.
Why is process management important?
Process management plays a key role in modern organisations as it contributes significantly to increasing efficiency, quality and competitiveness. This holistic approach to controlling work processes enables companies to successfully pursue their goals and adapt flexibly to constantly changing market conditions.
Goals of process management
The goals of process management include:
- Increased efficiency : Process management makes it possible to make processes more efficient by eliminating unnecessary steps or interruptions. This means that tasks can be completed faster and with fewer resources.
- Increased quality: Continuous monitoring and optimisation of processes, helps to improve the quality of products and services. Errors and irregularities can be identified and corrected at an early stage, leading to higher customer satisfaction.
- Increased flexibility : Through process management, processes can be designed so that they can be adapted to changing market conditions and customer requirements. This increases a company’s flexibility and adaptability.
- Reduced costs : Efficient processes and elimination of waste help reduce operational costs. A critical factor in all businesses.
- Improved interfaces : Process management promotes collaboration and communication between different departments and teams. This creates seamless interfaces, which contributes to a more effective overall organisation.
- Standardised processing: The introduction of clear process standards makes it possible to design tasks and work processes consistently and comprehensibly. This leads to greater predictability and quality of results.
By specifically pursuing these sub-goals, process management can help to significantly increase the overall performance and competitiveness of a company.
Advantages of process management
Process management offers a variety of benefits for organisations. One of the most important advantages is the increase in productivity. This is done by optimising processes, eliminating unnecessary steps and using resources more efficiently. At the same time, process management helps reduce errors by making it possible to identify and correct errors and irregularities at an early stage.
Another effect is the acceleration of processes. Efficient processes enable tasks to be completed more quickly, reducing turnaround times and increasing responsiveness to customer requests. This also contributes to increasing employee satisfaction, as clear responsibilities and work processes increase the effectiveness of employees and promote their commitment.
Process management also increases the competitiveness of companies because they can react more flexibly to market changes. The transparency and accountability created by process management, enable better planning of projects and activities, whilst long-term strategic goals can be better pursued.
Another important advantage is risk minimisation. Process management helps companies comply with legal regulations and quality standards, thereby minimising the risk of legal problems and quality problems. Overall, process management contributes significantly to increasing the effectiveness and efficiency of organisations, reducing costs and improving the quality of products and services. These qualities make process management a business-critical tool for modern businesses.
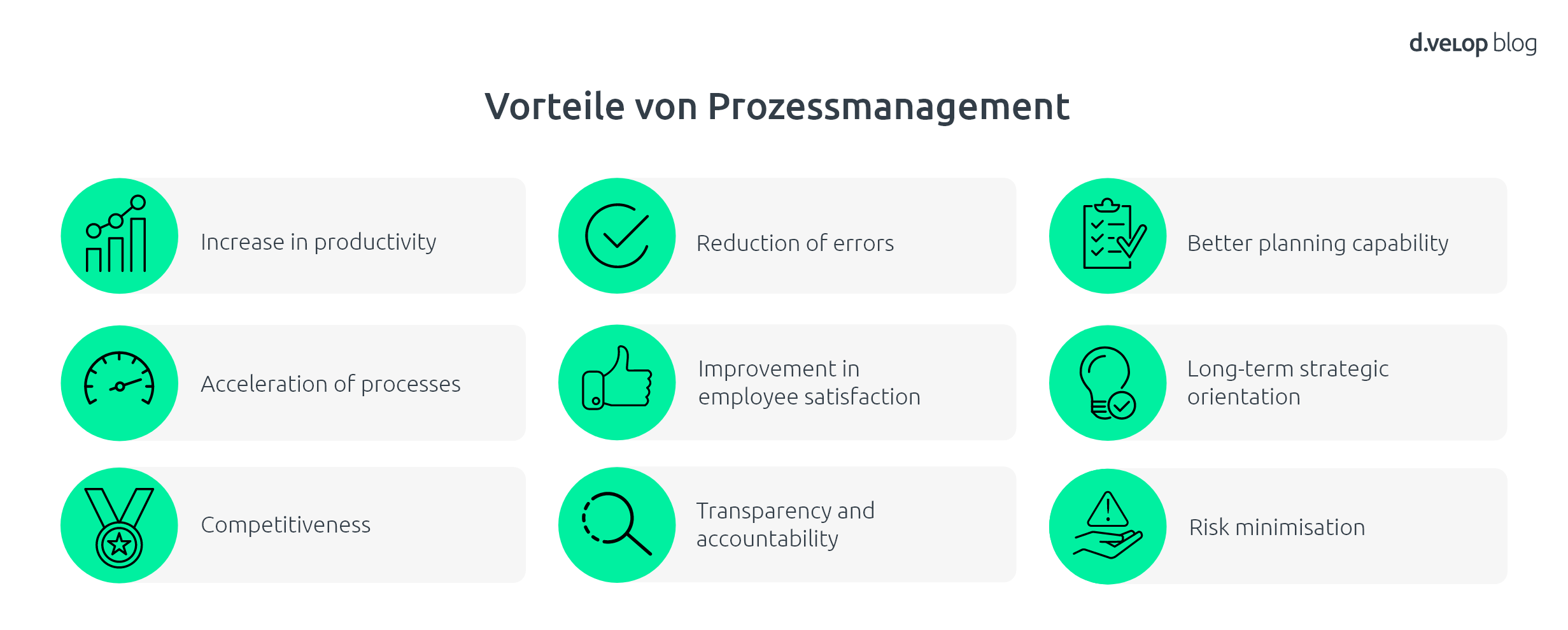
What process management methods are there?
There are many different methods in process management. Which one is best suited for your company depends, on factors such as: the industry it belongs to and the size of the company.
The most common process management methods
- Business Process Model and Notation (BPMN) is a standardised modelling language that makes it possible to represent business processes in diagrams. It provides a visual and consistent method for documenting and communicating processes.
- Business Process Reengineering (BPR) focuses on radical redesign of processes, to achieve efficiency gains and quality improvements. This approach often aims to completely redesign processes.
- Lean Six Sigma is a method that combines Lean principles for streamlining processes with Six Sigma methods for reducing errors. It aims at continuous improvements.
- Total Quality Management (TQM) focuses on continuously improving the quality of products and services. It integrates quality awareness into all aspects of the organisation.
- Kaizen is a Japanese philosophy of continuous improvement that aims to take small steps in daily work to create long-term positive changes.
- Scrum is an agile project management method, used to develop products and services efficiently and flexibly. It emphasises collaboration and short development cycles.
- Agile process management is an extension of agile methods to business processes. It aims to adapt processes to changing needs and markets, promoting collaboration and continuous delivery of value.
- ISO 9001 is an international standard for quality management that helps companies establish effective processes and increase customer satisfaction.
- Process mining uses data analysis to visualise the actual execution of processes and uncover weak points and optimisation potential.
- Kanban is a visual method for controlling workflows and improving process efficiency.
Various techniques can be used to check how well processes work, assessing both their quality and their efficiency. As an example: using key figures for process performance, which can then be compared with your own specifications (internal/external).
Basic approach to process management in 4 steps
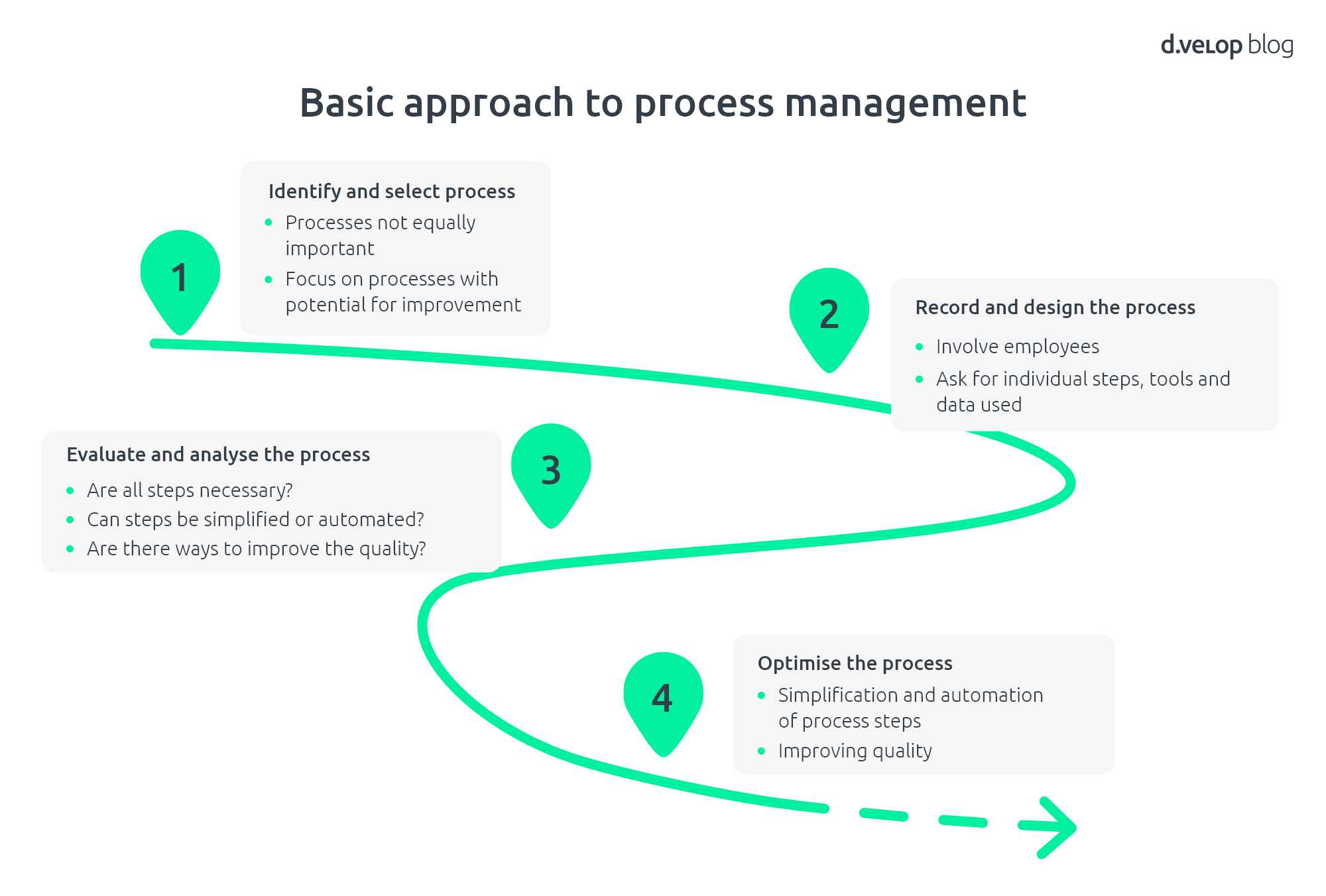
Step 1: Identify and select process
Not all processes in a company are equally important. First, focus on the processes where you see great potential for improvement. Such as:
- take a lot of time
- often cause errors
- used by many employee
- are important for customers
Step 2: Record and design the process
To understand a process, you have to describe it precisely. To do this, you should speak to the employees who are carrying out the process. Ask them about the steps, tools used, data involved and issues.
Step 3: Evaluate and analyse the process
Once you understand the process, you can evaluate it. You should answer the following questions:
- Are all steps necessary?
- Can steps be simplified or automated?
- Are there ways to improve the quality?
Step 4: Optimise the process
Based on your analysis, you can now optimise the process. You can take the following measures:
- Simplifying process steps
- Automation of process steps
- Improving quality
The newly optimised process should also be checked regularly. You should answer the following questions:
- Is the process working as planned?
- Are there new or further opportunities for improvement?
Conclusion: Process management is of great importance for organisations
Process management is an important approach for organisations to optimise their processes and thus, increase their efficiency and effectiveness. By systematically analysing and improving processes, companies can reduce costs, improve customer satisfaction and strengthen their competitiveness.
An important step in process management is the digitalisation and automation of processes. By using digital tools and automation solutions, companies can make their processes more efficient and error-free.
The d.velop process studio helps automate processes – without IT skills
The d.velop process studio enables specialist departments to visualise and automate their own processes. The specialist department designs its process and indicates in the d.velop process studio, which information is needed at which points. The IT administrator then ensures that the necessary information from external systems is integrated into the appropriate places.
Book software demo! 💻
Experience the power of d.velop’s software with a personalized live demo, easily requested with just a few clicks. Watch as the software comes to life before your eyes and ask any questions you may have in real-time.